At TIKA Technologies, we work in small teams. Every team member fully understands our client’s needs. We understand the relevant concepts and terminology. We are fanatically dedicated to defining our terms. Among all involved in the development process, we insist on clear prompt communications.
Here are examples of documents and presentations we created so everyone on our team understood our client’s needs. Working with our clients, we learned the concepts of Overall Equipment Effectiveness, the various terms used within the industry and agreed on our naming conventions.
Here are slides from our client meeting during which we reviewed with our understanding of OEE and our proposed naming conventions.
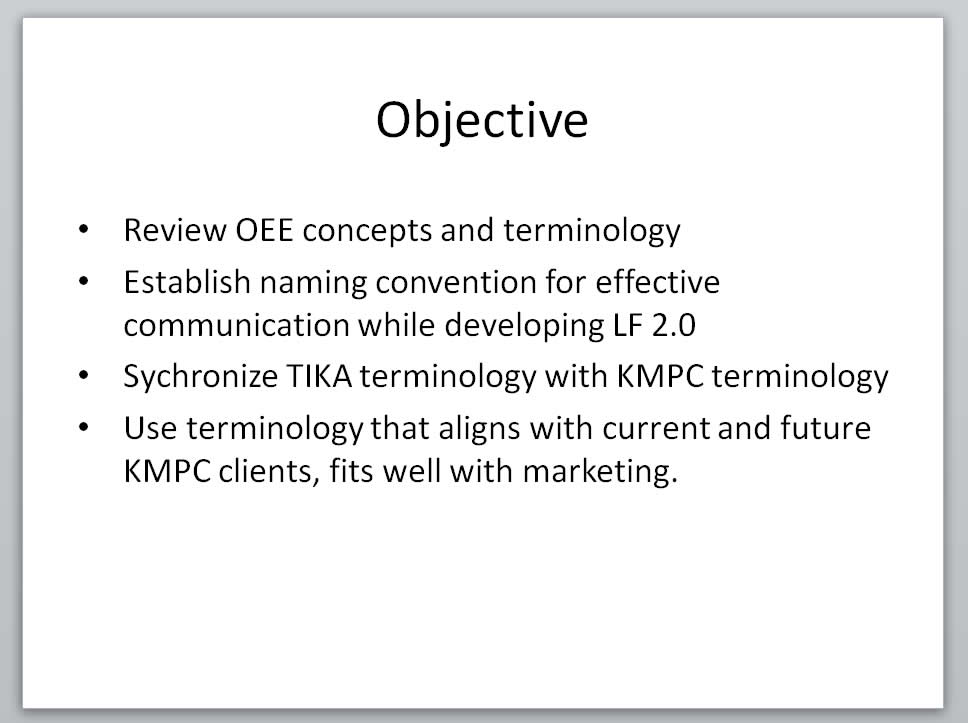
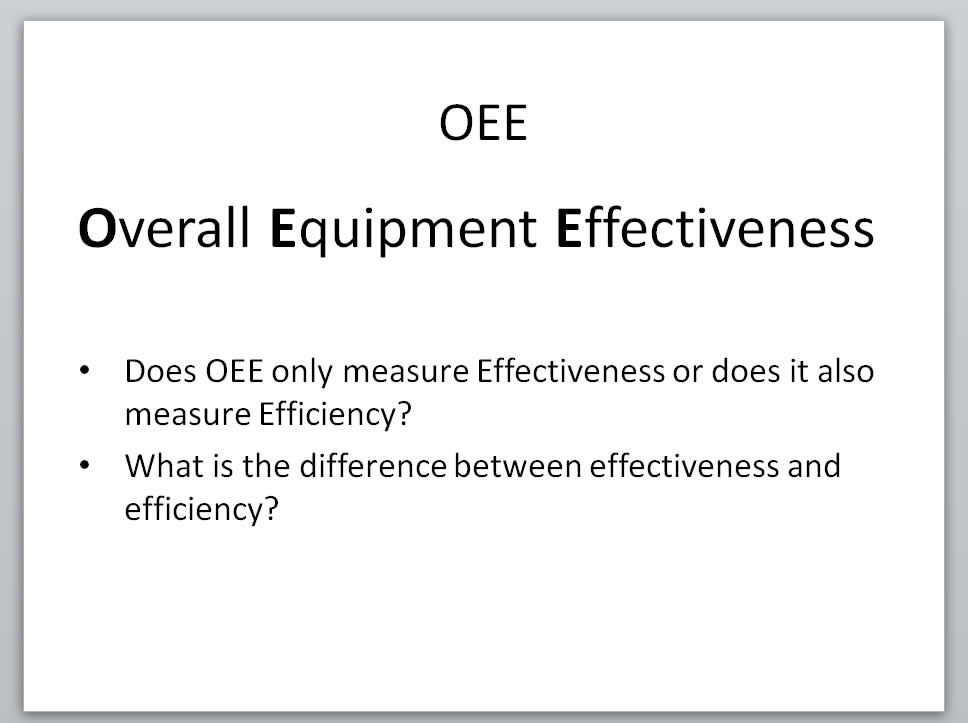
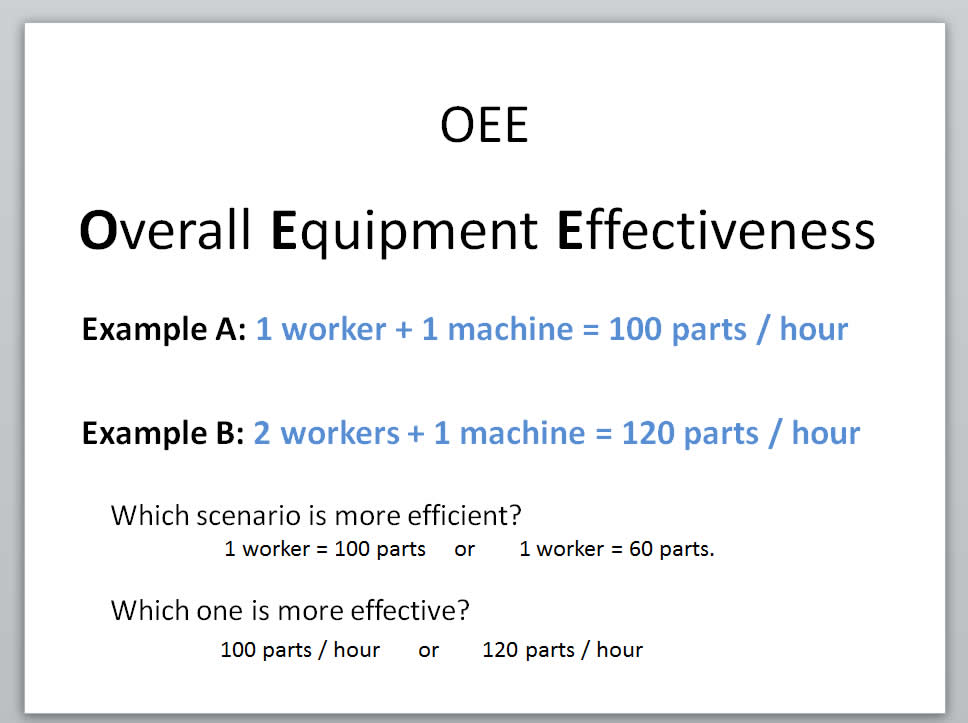
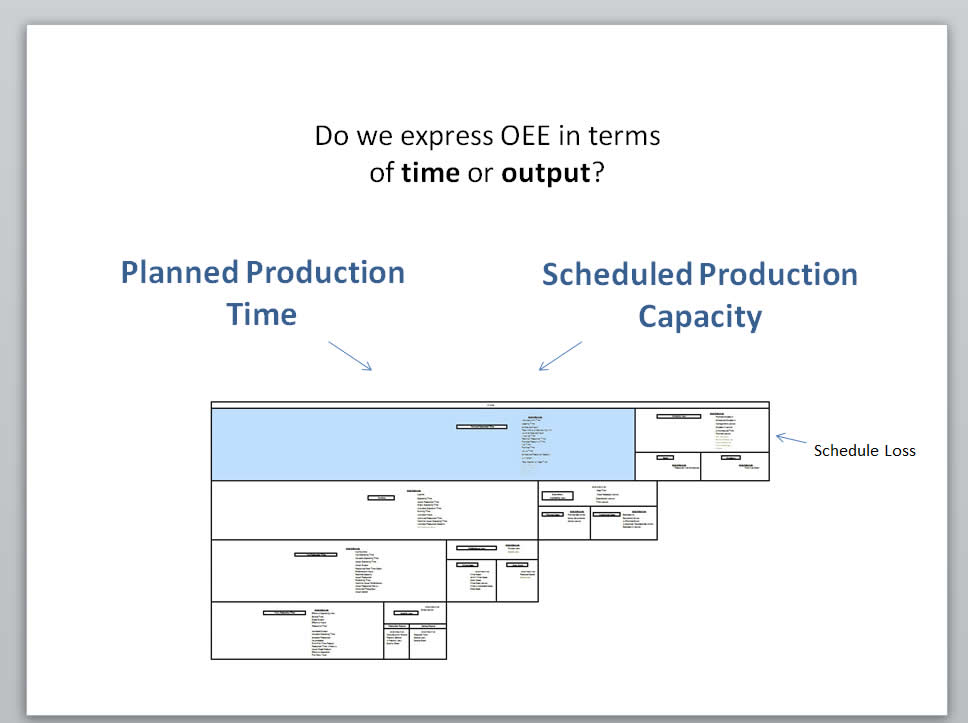
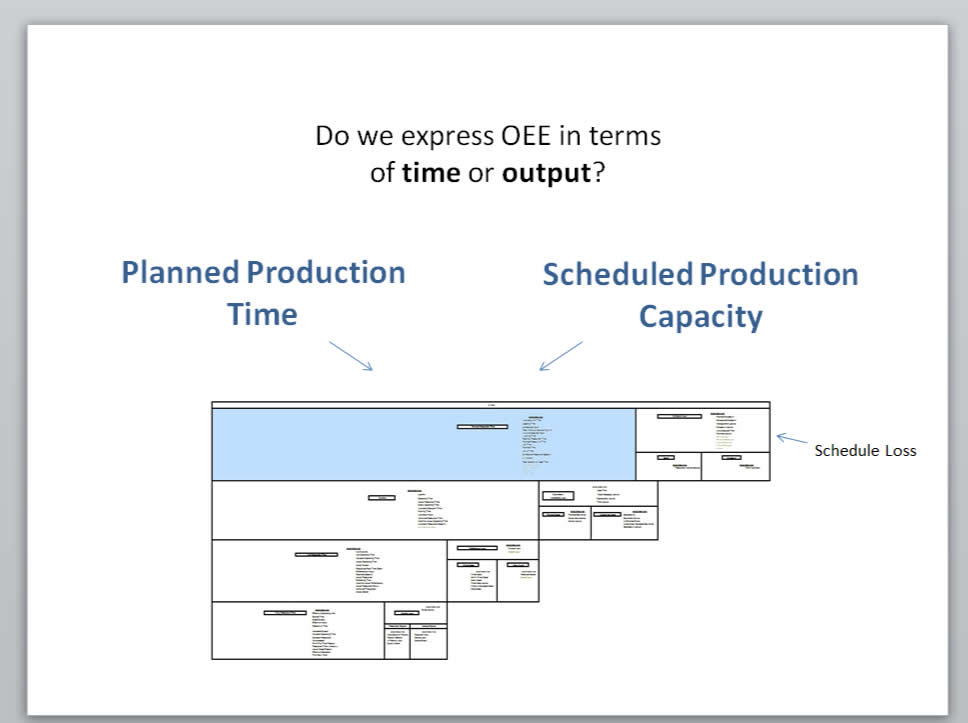
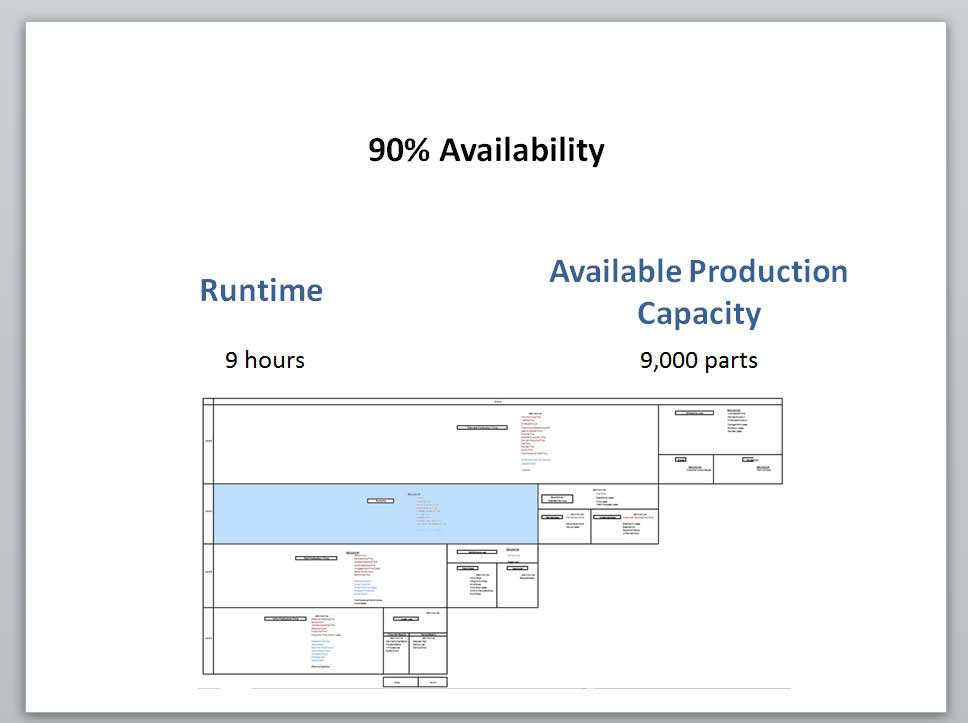
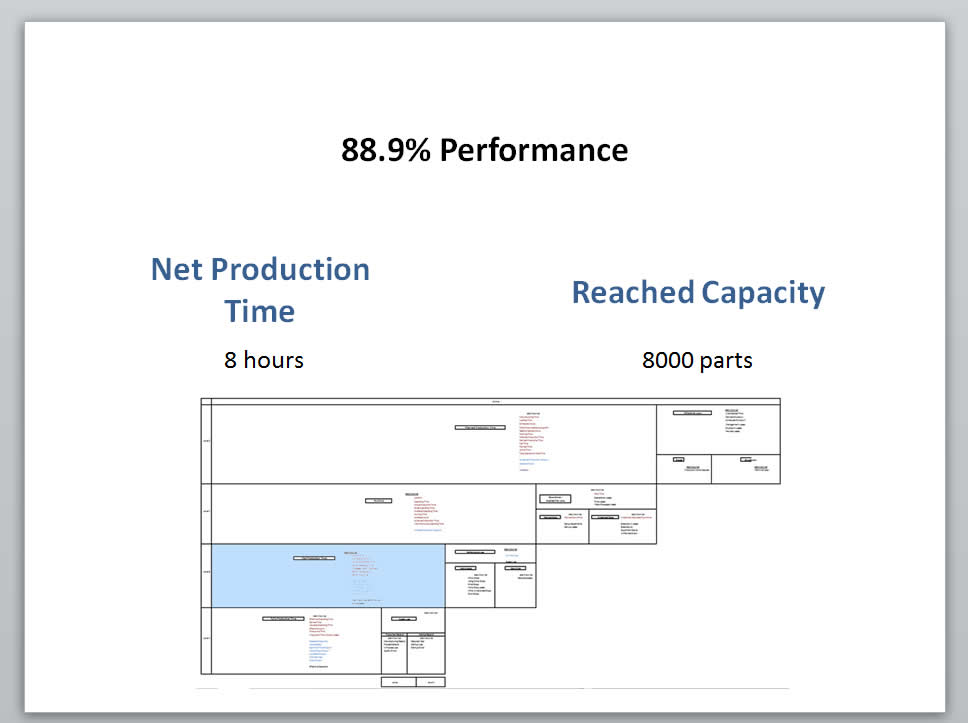
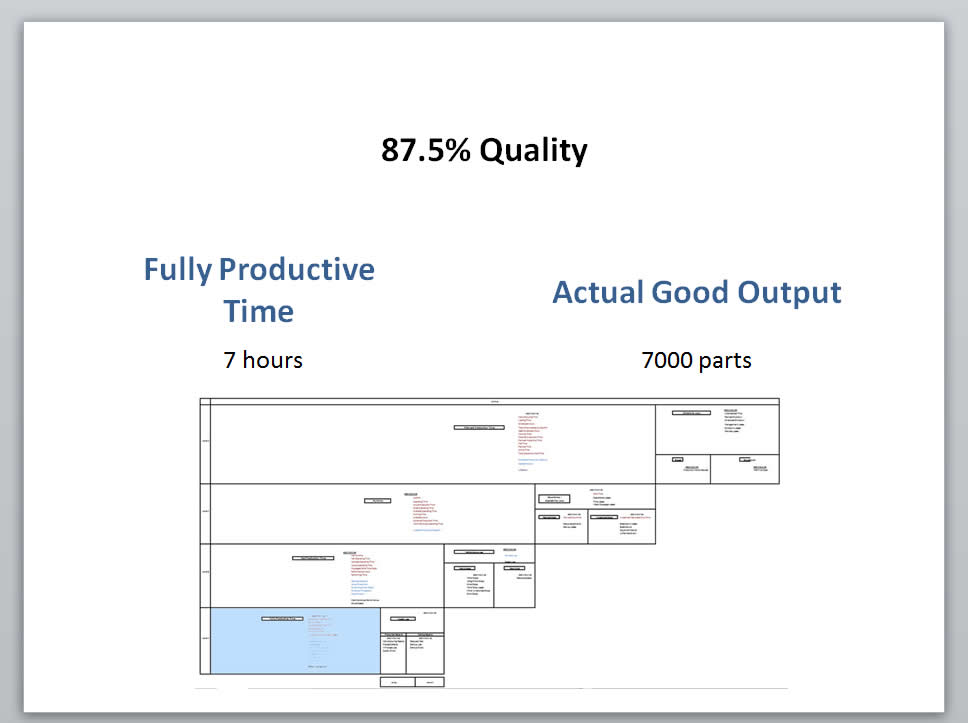
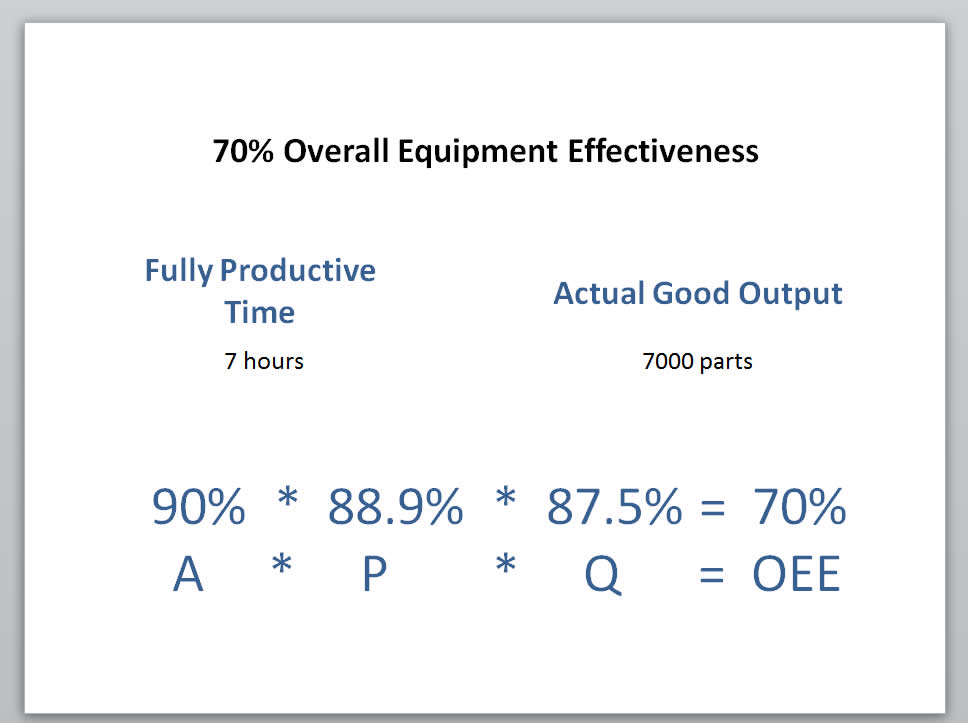
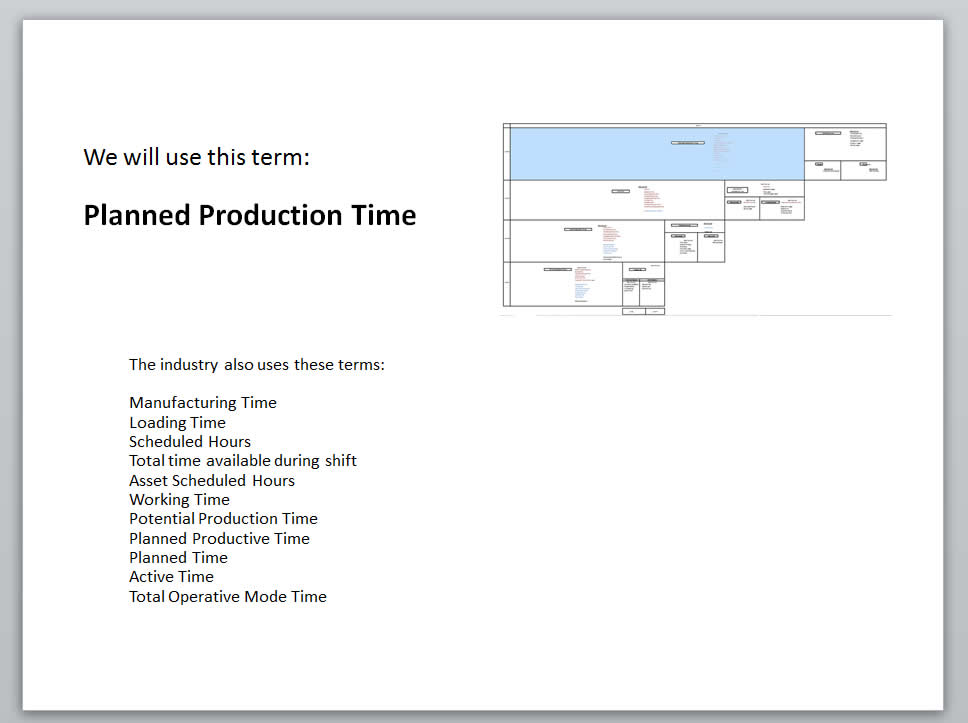
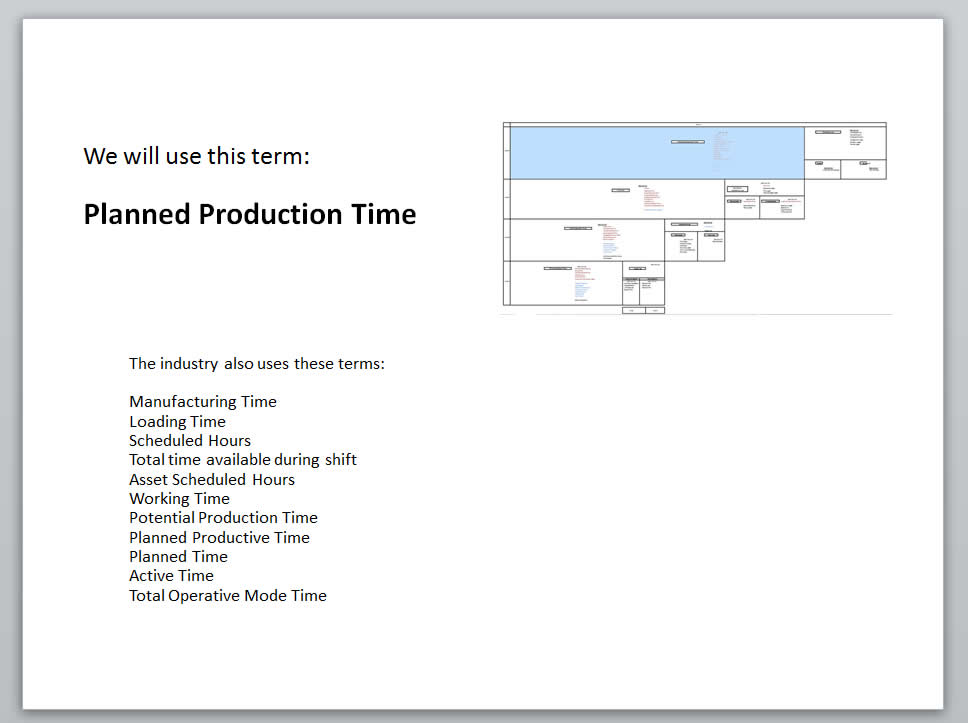
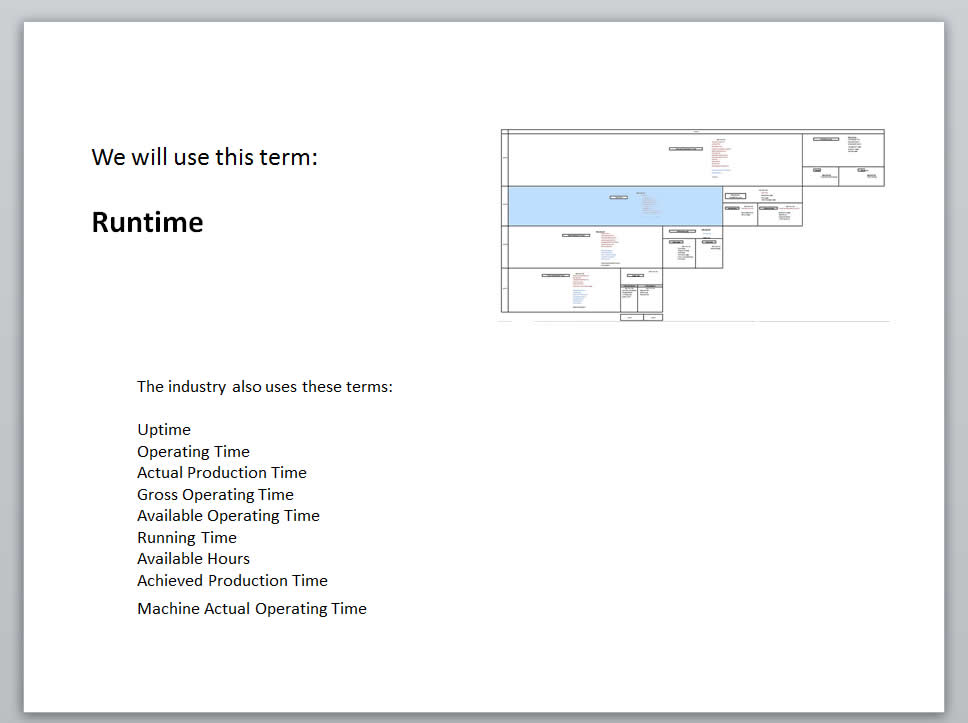
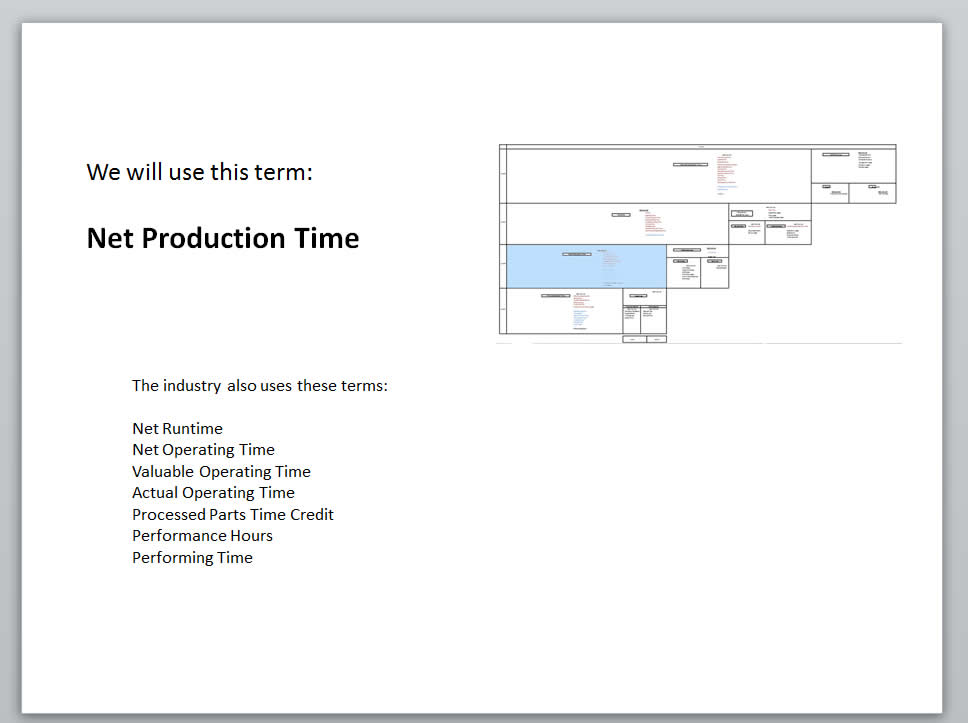
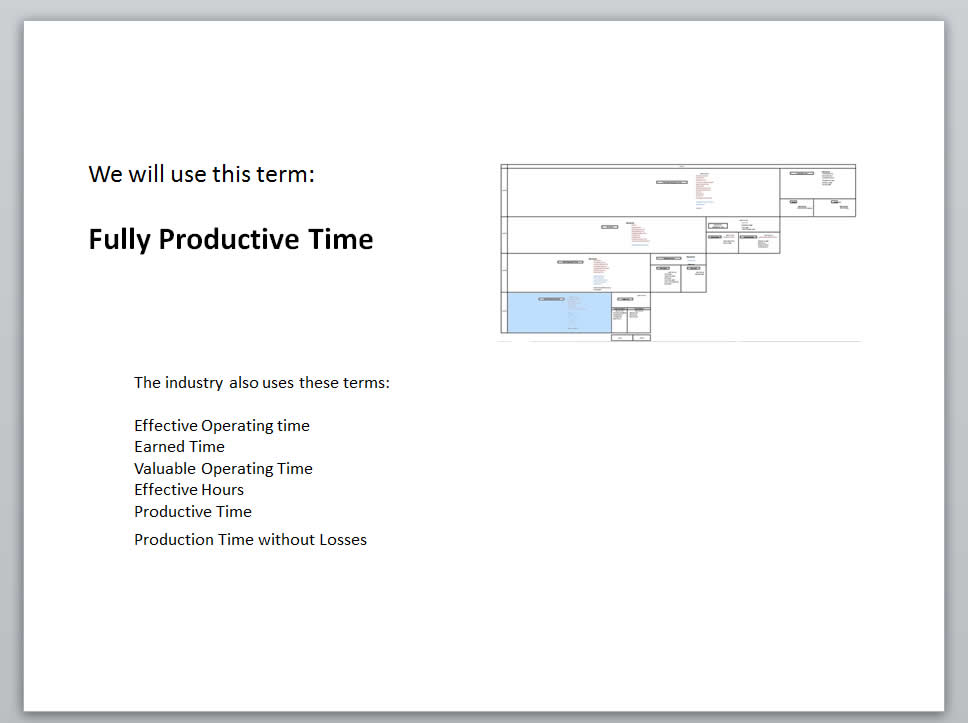
Then we needed to explain a common source of confusion in OEE. When the factory is shut down for the night, the machines are stopped and that time is planned. However that is NOT called a Planned Stop. We used race cars and the pitstop for an analogy. When cars are in a race, you want the pitstop to be as quick as possible. During Planned Production Time, whenever a machine is stopped, even if planned, that stop should happen as quickly as possible.
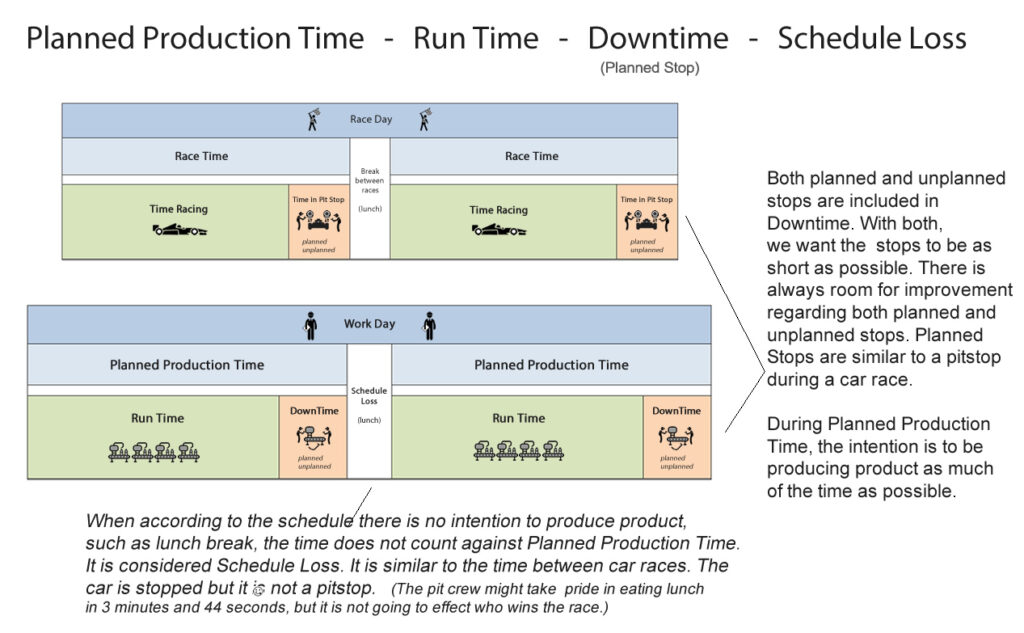
With the distinction of Planned Stop understood, we agreed on terms we would use when discussing downtime and losses. The term „shut down“ was reserved for Schedule Loss. The word „stop“ was reserved for Downtime. The word „idling“ was reserved for Performance Loss.
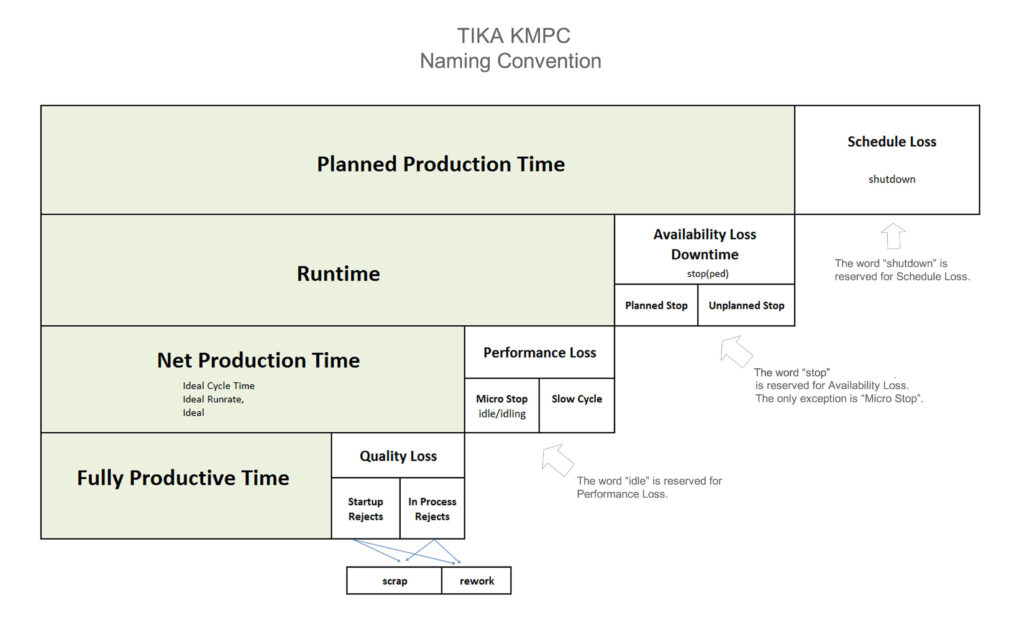
With the above concepts and terms fully understood, our communications were clear and consistent. We could also effectively onboard new team members.